- Get link
- X
- Other Apps
Imagine a manufacturing world without unexpected downtime or production line disruption, production lines that adjust easily to changing demands, and new products making their debut in stores within days! That vision doesn’t exist yet, but digital transformation in manufacturing promises it a reality today; manufacturers face increasing operational costs as supply chains become unpredictable, customers demand faster delivery of more tailored offerings, and operations are under increased strain to meet them.
Digital Transformation (DT) offers the solution. More than just new tech, DT involves fundamentally altering how businesses run using data collection, connectivity, and automation systems to build smarter, more agile and resilient systems – part of Industry 4.0, which leads to smart manufacturing.
Digital transformation has become essential to manufacturers’ business strategies; no longer an optional practice, companies require digitalization in order to gain top efficiency and innovation and remain globally competitive. In this blog post, we’ll look at why manufacturers are adopting this path toward digitalization – key technologies driving change as well as its actual benefits – with clear guidance for your digital journey.
Core Technologies Driving Manufacturing Digital Transformation
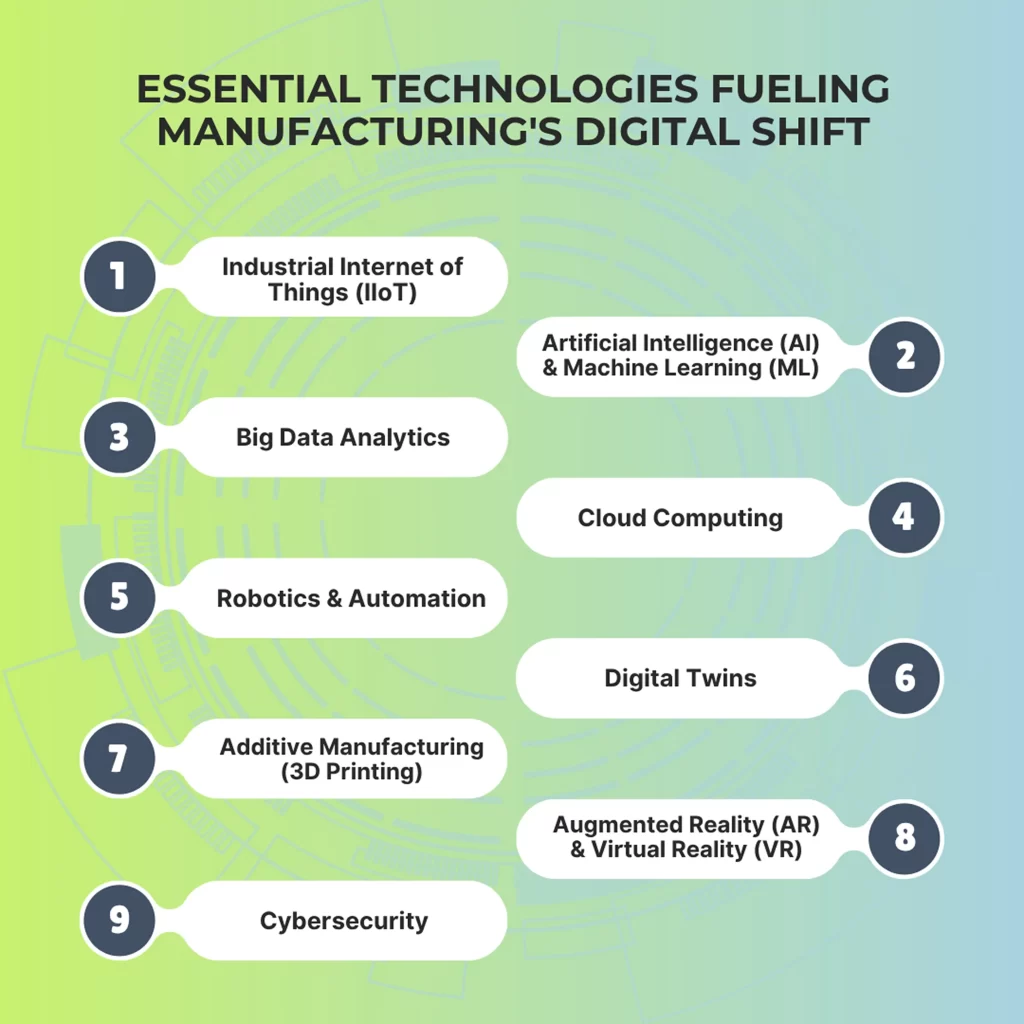
Industrial Internet of Things (IIoT)
Industrial IoT (Industrial Internet of Things, IIoT, is essential to connected factories. By installing intelligent sensors and devices onto machines on production lines and across a factory floor, this network constantly generates real-time data regarding machine performance, environmental conditions, and material flow. This provides excellent visibility for manufacturers by connecting these assets and giving proactive monitoring. Predictive maintenance helps reduce downtime while production processes become much more efficient. Adding smart sensors transforms old, separate machines into intelligent assets capable of communicating together to form one comprehensive data-driven manufacturing system, which forms a key part of digital transformation in advanced manufacturing industries like advanced manufacturing.
Artificial Intelligence (AI) and Machine Learning (ML)
AI and machine learning (ML) technologies form the cornerstone of intelligent manufacturing, helping systems analyze vast volumes of data sourced by IoT devices and other sources. AI helps systems recognize patterns missed by humans that influence forecasting demand forecasting as well as resource allocation optimization, while machine learning enables machines to improve over time without constant programming needs – this means self-optimizing production lines using intelligent robots as well as improvements to decision making in every step from automated inspections to fine-tuning energy use; AI/ML systems offer both intelligence as well as increased adaptability.
Big Data Analytics
Big Data Analytics harnesses massive quantities of manufacturing data to discover valuable insights, from structured ERP/MES systems and sensor/video feeds through to customer reviews and unstructured sensor feeds such as video. Advanced analysis helps manufacturers pinpoint inefficiency sources while also discovering emerging trends; supply chain logistics become smoother; products become personalized more readily – all due to Big Data Analysis’ transformation of raw information into tangible steps for action that enable smart, data-driven decisions which improve operations while cutting costs and speeding innovation.
Cloud Computing
Cloud computing offers manufacturers the robust infrastructure required for digital manufacturing, from data processing and storage needs to application hosting and simulation running – without costly on-site servers! Manufacturers use cloud platforms instead, where applications, massive datasets, and complex simulations can all be hosted there along with real-time team collaboration across global teams; resource allocation can easily adapt according to production demands; scaleable resources can then be added or removed depending on production needs; it drastically lowers IT costs while making data more easily accessible, creating a solid basis for connecting various digital technologies smoothly while supporting digital transformation efforts while creating digital transformation and manufacturing competitiveness.
Robotics & Automation
Robots have long been recognized for improving productivity, precision, and safety in industry settings. Modern industrial robots feature cutting-edge sensors and AI that enables them to complete repetitive, dangerous or exact tasks more quickly and accurately than humans could manage alone. Furthermore, collaborative robots (cobots) have become an increasingly popular form of automated systems since these allow both humans and machines to collaborate side-by-side, increasing output while decreasing errors while improving quality. Operations run seamlessly, greatly increasing overall efficiency while decreasing operational costs significantly.
Digital Twins
A digital twin is an online representation of tangible assets or processes that constantly update with data from its physical counterpart, often called its twin or physical “Twin.” For manufacturing purposes, a dynamic digital model could represent any asset from machines and production lines to entire factories – this provides manufacturers with access to different scenarios without stopping live operations; they predict failures while optimizing performance while giving a complete real-time view into operations; this enables proactive problem-solving while decreasing downtime while speeding product development through virtual testing – providing a full real-time real-world view into operations allowing proactive problem-solving as well as unveiling new pathways of digital transformation within manufacturing! This technology represents new adoption paths of digital transformation within manufacturing industries that were once unseen.
Additive Manufacturing (3D Printing)
Additive Manufacturing (3D Printing) is an impressive technological revolution. This cutting-edge form of 3D printing creates 3-dimensional objects layer by layer from digital designs using additive manufacturing; unlike traditional methods, it adds material rather than subtracts it, which enables complex shapes. Furthermore, 3D printing supports customized parts production on-demand as well as fast prototyping using fast prototyping printers, printed lightweight tools or components, supporting localized production while shortening delivery times and cutting material waste. It also opens new possibilities in product customization across many industries – thus fueling innovation across many sectors!
Augmented Reality (AR) & Virtual Reality (VR)
AR and VR technologies are revolutionizing how manufacturers view and interact with the physical world. AR places digital information directly over physical surroundings, aiding technicians with maintenance through real-time instructions or seeing hidden parts through smart glasses. VR creates fully immersive virtual worlds to facilitate realistic training on complex machines as well as product design reviews with remote teams as well and factory tours that help optimize planning and optimization; worker training improves, collaboration increases, and errors are reduced by providing easy access to critical data. These technologies improve worker training while simultaneously increasing collaboration by giving access to essential data more easily – as well as improving worker training and boosting collaboration while providing easy access to critical data via smart glasses compared with conventional methods.
Cybersecurity
Manufacturing systems today rely heavily on digital tech and require strong cybersecurity measures in order to safeguard industrial control systems, production data, operations and intellectual property, as well as prevent cyber threats such as ransomware and data breaches. Effective manufacturing cybersecurity requires multiple layers of protection: this may include secure networks with access controls; employee training on best cybersecurity practices is equally vital; threat intelligence analysis provides essential intelligence updates, while regular monitoring ensures strong manufacturing operations that stand the test of time.
Tangible Benefits of Digital Transformation
A. Operational Efficiency
Digital transformation will improve how efficiently your organization operates in several key ways. First, it reduces downtime with predictive maintenance powered by smart sensors and data analysis, allowing machines to notify assistance teams that they require service before breaking down completely. That means fewer unexpected stops and much smoother production. Next comes Optimized Resource Utilization. Digital tools offer real-time insights into energy use, raw material consumption, and labour allocation and can even allow fine-tuning of these elements. As a result, less resources are wasted while better use is made of those available to us.
Furthermore, you witness improved Quality Control thanks to artificial intelligence (AI). AI detects defects early on, sometimes before they even form entirely, which reduces rework while improving final product quality. Finally, digital processes lead to Faster Time-to-Market by streamlining workflows and automating tasks quickly, moving new products from design through delivery faster – providing companies with a significant competitive advantage in speed.
B. Cost Reduction
Digital transformation in manufacturing offers significant cost-cutting potential. First of all, operational expenses decrease through automation taking on more tasks by itself, while predictive maintenance reduces repair costs while energy efficiency lowers utility bills. All these elements contribute to an efficient operation. Digital solutions also facilitate reductions of waste and rework through improved quality control, optimized processes and reduced production errors, resulting in fewer defective goods. This saves both materials and labour that would have otherwise gone to waste and minimizes Inventory Holding Costs. Through accurate demand forecasting and just-in-time production enabled by digital tools, precise demand forecasting can lead to reduced excess inventory storage needs, which frees up capital and warehouse space. These are two distinct adoption paths of digital transformation in manufacturing, which yield financial returns.
C. Enhanced Supply Chain Management
Digital transformation offers many core benefits to companies of any kind, one being creating more resilient and transparent supply chains. You gain greater visibility into all stages of production, from raw material procurement through final delivery – which helps track goods quickly while anticipating any issues along the way. Thus, digital tools help improve responsiveness to disruptions: when problems such as supplier delays or logistics issues arise, digital tools enable faster identification and responses so you can reroute or find alternatives faster. Finally, better supplier collaboration: digital platforms facilitate seamless information sharing among partners, which strengthens relationships while improving communications efficiently, creating an efficient supply chain that benefits all involved parties involved.
Conclusion
Digitizing manufacturing has already transformed the industry, as evidenced by its profound effects. From increasing efficiency and cutting costs, to driving innovation and strengthening supply chains – its effects are undeniable and manufacturers must adapt digital transformation practices if they hope to remain competitive in today’s globalized environment.
Do not delay starting on your digital transformation journey – do it today. Explore technologies discussed, identify pain points and consider potential solutions. Echoinnovate IT’s expert guidance and tailored solutions can assist manufacturing companies in successfully managing this transformation; reach out now so we can unlock all your business’s potential! The future looks bright – yet digital.
- Get link
- X
- Other Apps
Comments
Post a Comment